-
-
What are the benefits of implementing a Warehouse Management System (WMS)?
-
Is it necessary to reconfigure the warehouse floor plan for better storage?
-
How do properly sized picking containers contribute to efficient warehouse storage?
-
Why should I consider seasonal inventory storage in my warehouse?
Looking to optimize your warehouse space? Stack racks are the answer! These versatile cantilever storage options help maximize warehouse efficiency, enhancing organization and accessibility. In this listicle, we’ll dive into the top reasons why stack racks are a game-changer for warehouse storage, helping space utilization and offering options.
From cost-effective utilization of floor space to their flexibility in accommodating various inventory types and product storage, stack racks revolutionize the way warehouses operate. We’ll explore their durability and ease of assembly, making them an indispensable asset for any storage facility. Get ready to discover how stack racks can streamline your operations, improve warehouse space utilization, and elevate efficiency like never before.
Scroll down for reviews of our top picks that will take your warehouse storage and space utilization to new heights!
1. Install a Mezzanine
By installing a mezzanine, warehouses can effectively utilize vertical space for additional storage. This solution creates a new level for storing lightweight items, optimizing the available storage density within the warehouse.
Mezzanines offer a distinct advantage by maximizing warehouse space without the need for costly expansions or relocations. This option is particularly beneficial for businesses experiencing growth and requiring more warehouse space utilisation without incurring significant construction expenses.
In addition to providing extra storage room, mezzanines also allow companies to maintain efficient workflows by keeping frequently used items easily accessible on the main floor while utilizing the elevated platform for less frequently accessed inventory.
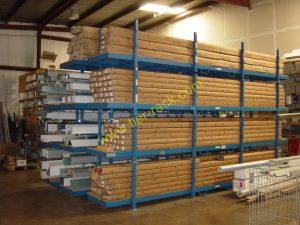
Furthermore, installing mezzanines can be an excellent solution for warehouses that store seasonal or slow-moving products as it provides dedicated space without compromising accessibility to high-demand items.
2. Reduce Aisle Width
Optimizing floor space by narrowing aisle width is an efficient way to increase storage capacity and enhance overall warehouse efficiency. By minimizing unnecessary aisle space, businesses can make the most of their square footage for storing goods and products.
-
Narrow aisles allow for more racks to be installed within the same area, effectively increasing the storage capacity without expanding the warehouse.
-
Reducing aisle width also contributes to a more organized and streamlined workflow, as it minimizes the distance traveled by workers when retrieving items from shelves, improving warehouse space utilisation and storage space.
-
Many modern stack rack systems are designed with narrow aisles in mind, utilizing vertical space efficiently without compromising accessibility.
In addition to these benefits, companies that implement narrower aisles often report significant improvements in inventory management and order fulfillment processes. For example, a study conducted by a leading logistics company found that reducing aisle width resulted in a 20% increase in storage capacity while maintaining operational efficiency.
3. Increase Rack Height
Maximizing warehouse space is crucial for efficient storage and operations. Utilizing taller stack racks can significantly enhance vertical storage space, allowing warehouses to accommodate more inventory without expanding their physical footprint.
By increasing the height of stack racks, warehouses can optimize their capacity, making it possible to store a larger volume of goods within the same floor area. This approach is particularly beneficial for facilities with limited space or those aiming to avoid costly expansions.
Taller storage racks also contribute to better organization and accessibility. With increased vertical storage, items can be stored in a more structured manner, promoting easier retrieval and inventory management processes.
Moreover, higher rack systems are designed with safety features that ensure stability at elevated heights. Advanced engineering and materials enable these racks to withstand heavy loads while maintaining structural integrity, providing a secure environment for storing products.
For example, by opting for storage rack systems that offer adjustable heights or customizable configurations based on specific inventory needs, warehouses can tailor their storage solutions to maximize efficiency and meet evolving demands.
4. Consider Seasonal Inventory Storage
Planning for seasonal inventory fluctuations is crucial for optimizing warehouse storage. By forecasting seasonal demands, businesses can allocate specific areas for the rotation of seasonal stock, ensuring efficient use of space and resources.
Adjusting the storage layout based on seasonal inventory requirements allows for better utilization of available storage capacity. For example, during peak seasons, products with high demand can be strategically placed in easily accessible areas to minimize labor costs and time spent retrieving items.
By considering seasonal inventory storage needs, businesses can implement efficient storage solutions that cater to fluctuating product storage demands. This approach not only maximizes the usage of available storage units but also enhances overall storage density by adapting to changing product volumes throughout the year.
For instance, a retailer preparing for holiday season sales may prioritize storing festive merchandise closer to shipping docks or packing stations to streamline order fulfillment processes during peak periods. This targeted allocation of space reduces handling time and improves operational efficiency during high-demand periods.
5. Manage Inventory Levels
To prevent overstocking or understocking, it’s crucial to keep a close eye on inventory levels. Efficient inventory management practices can help optimize space usage and ensure that the right amount of goods is always available for order fulfillment.
Utilizing real-time data is essential in maintaining optimal inventory levels. By leveraging advanced technology and automated systems, businesses can accurately track stock movements, anticipate demand fluctuations, and make informed decisions about stocking strategies.
Implementing these strategies not only ensures smooth operations but also directly impacts customer satisfaction. When products are readily available without excessive wait times, it enhances overall customer experience and fosters loyalty.
6. Check for Underutilized Space
Regular assessments of the warehouse can reveal underutilized areas, unlocking additional storage potential. By identifying and repurposing these spaces, overall efficiency and space utilization can be significantly improved.
Conducting routine evaluations allows for the optimization of floor space by eliminating unused or inefficiently used areas within the warehouse. This process ensures that every square foot is contributing to the storage capacity, ultimately maximizing available space.
For instance, a study conducted by a leading logistics company found that implementing regular checks for underutilized space led to a 20% increase in overall storage capacity within their warehouses. This resulted in substantial cost savings and improved operational efficiency.
7. Use Properly Sized Picking Containers
Selecting picking containers that fit efficiently within the storage system is crucial for optimizing warehouse operations. By choosing appropriately sized containers, you can streamline the picking process and ensure seamless integration with storage racks.
Properly sized picking containers help in maximizing space utilization within the warehouse. This ensures that small parts and items are stored securely without wasting valuable shelf space.
Using containers of suitable size also contributes to safety by preventing overloading or underutilization of storage racks. It helps in maintaining a balanced weight distribution, reducing the risk of accidents due to imbalanced loads.
For example, using small bins for storing tiny items and larger bins for bulkier products can significantly enhance efficiency during order fulfillment processes. It allows pickers to locate and retrieve items swiftly, contributing to a more productive workflow.
8. Reconfigure Your Warehouse Floor Plan
Redesigning the layout of your warehouse can significantly impact its efficiency and storage capacity. By optimizing the floor plan, you can enhance workflow and accommodate changing storage needs.
Reconfiguring the warehouse floor plan allows for better utilization of warehouse space, maximizing every square foot to fit in more inventory or equipment. This not only increases storage capacity but also improves overall warehouse efficiency.
A well-thought-out layout ensures that the physical footprint of the warehouse is used effectively, minimizing wasted space and streamlining operations. For instance, strategically placing high-demand items closer to the shipping area can expedite order fulfillment processes.
Businesses with evolving needs can benefit from a flexible floor plan that adapts to changes in inventory size or types of products stored. Whether it’s adding new shelving units or creating designated areas for specific product categories, an adjustable layout supports scalability.
9. Implement a Warehouse Management System (WMS)
Integrating a Warehouse Management System (WMS) is crucial for optimizing warehouse operations and space utilization. WMS software allows companies to efficiently control inventory, manage shipping processes, and enhance overall organization within the warehouse.
By utilizing the features of a WMS, such as real-time inventory tracking and automated workflows, companies can significantly improve their warehouse organization and operational efficiency. For instance, WMS enables better coordination between different areas of the warehouse, reducing the time spent on locating items and improving order fulfillment accuracy.
Moreover, implementing a comprehensive WMS solution can lead to substantial benefits for company operations. According to research by Aberdeen Group, organizations with an effective WMS experience an average of 22% improvement in inventory accuracy and a 17% increase in shipping accuracy.
10. Use Automated Storage and Retrieval Systems (AS/RS)
Incorporating Automated Storage and Retrieval Systems (AS/RS) technology in warehouse management can significantly enhance efficiency by automating inventory handling and storage processes. AS/RS solutions utilize automation to retrieve, store, and manage inventory items, reducing the need for manual labor while ensuring accuracy.
By implementing AS/RS technology, warehouses can optimize space utilization by storing items vertically using shelving units that are accessible through automated methods. This not only maximizes the use of available space but also ensures that goods are stored according to set standards, leading to improved organization and accessibility.
The integration of AS/RS technology enables warehouses to streamline their operations by minimizing human intervention in the retrieval and storage of goods. This results in faster turnaround times for order fulfillment as well as reduced errors in inventory management.
Furthermore, AS/RS systems provide valuable data insights into warehouse operations, allowing businesses to make informed decisions regarding stock levels, replenishment schedules, and overall process optimization.
Summary
Congratulations on reaching the end of our guide to optimizing warehouse storage with stack racks! By implementing the strategies outlined in this post, you can maximize your warehouse space, improve efficiency, and enhance overall productivity. From installing a mezzanine to utilizing automated storage systems, these practical tips offer actionable solutions to elevate your warehouse operations.
Now it’s time to take action. Assess your current warehouse setup, identify areas for improvement, and start implementing these strategies. Remember, a well-organized warehouse not only streamlines operations but also sets the stage for future growth. So, roll up your sleeves and get ready to transform your warehouse into a space that works smarter, not harder.
Frequently Asked Questions
How can I maximize warehouse space for storage?
To maximize warehouse space, consider installing a mezzanine, reducing aisle width, increasing rack height, checking for underutilized space, and using automated storage and retrieval systems (AS/RS). These strategies help optimize vertical and horizontal storage capacity efficiently.
What are the advantage of implementing a Warehouse Management System (WMS)?
Implementing a WMS offers benefits such as improved inventory accuracy, streamlined order fulfillment processes, enhanced labor productivity through better task allocation, real-time visibility into stock levels and locations. It also helps in optimizing space utilization and minimizing carrying costs.
Is it necessary to reconfigure the warehouse floor plan for better space utilisation and inventory levels?
Yes, reconfiguring the warehouse floor plan is essential to optimize available space effectively. By redesigning layouts based on inventory flow patterns and operational needs, you can enhance accessibility to items while maximizing overall storage capacity.
How do properly sized picking containers contribute to efficient warehouse storage and space utilization?
Properly sized picking containers play a crucial role in efficient warehouse storage by ensuring optimal use of shelf or rack spaces. They facilitate organized item placement which reduces wasted areas within shelves or racks while enhancing pick-and-pack operations’ efficiency.
Why should I consider seasonal inventory storage in my warehouse for business space utilization?
Considering seasonal inventory storage allows you to adapt your warehousing strategy based on fluctuating demand patterns. By segregating seasonal goods from regular stock, you can free up prime storage areas for high-demand items during peak seasons without compromising operational efficiency.